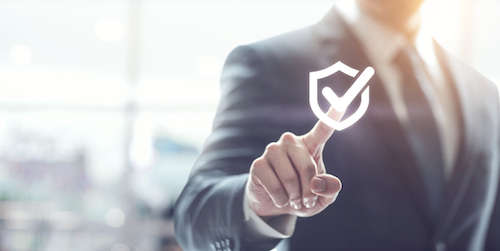
Increasing efficiency in your pet food production systems is a must. Increasing efficiency can mean many things. It might mean decreasing waste, lowering costs, improving speed, or increasing production. There are many ways to go about this. These improvements can also be difficult to compare or analyze. In this blog post, we’ll discuss a few of the most readily available process improvements specifically in pet food processing. These pet food processing improvements can help to decrease waste, improve process speed, and improve overall efficiency at your pet food production facility.
Process Improvements to Increase Efficiency in Pet Food Processing
Optimizing Liquid Coating Systems
Liquid coating systems for pet food present a number of challenges to pet food processing facility managers, as well as opportunities for improving efficiency. Pet food facilities working with liquid coatings that are high in fat content, like many dry pet food processing plants, often struggle with clogs and pressure backups. Liquid coating nozzles can easily become clogged in these situations, requiring frequent cleaning, maintenance and replacements. Overall, this requires downtime and eats into production time. Pressure backups also reduce the equipment’s lifespan. When clogged nozzles do not coat products evenly, this can also result in product defects and losses.
Comparing Liquid Coating Equipment
Finding the right liquid coating process and equipment for pet food production systems can increase the efficiency of this process dramatically. Your coating system must be designed to suit your liquid coating product, as well as the surrounding processes. The liquid coating must also have enough time and opportunity to evenly coat the product and properly absorb.
Considering alternative liquid coating solutions can help to optimize coating quality, reduce maintenance, and even speed up the process. Even making slight alterations to the mixing process, such as reducing screw conveyor flights or introducing pitched paddles can increase the mixing action and improve the uniformity of the coating. If the spray nozzles are consistently causing problems, consider a system that bypasses spray nozzles, such as a spinning disk atomizing system.
Automated Micro Ingredient Systems
Some pet food formulas require the addition of micro ingredients, such as vitamins and minerals. A reliable automated micro-ingredient system for pet food manufacturing systems can help to reduce waste, improve batching accuracy, reduce process time, and improve ingredient tracing. Adding ingredients by hand introduces the opportunity for waste and error. Automated micro ingredient systems allow you to measure ingredients quickly and exactly. With the right micro ingredient systems and tracking system integration, you can also save time on FSMA-required lot tracking.
Scale Calibration
An important aspect of an efficient micro ingredient system is accurate weighing devices. When weighing small amounts of ingredients, accuracy is essential. Be aware of effects that can make your load cells inaccurate, such as temperature changes, load cell creep, interference, or a lack of calibration. Keep in mind that small mistakes in measurements can add up; a minor weighing error with as little as .5% overuse ultimately means wasting .5% of the total product purchased.
FSMA rules require that pet food processing facilities track and trace ingredients, just like food for human consumption. Automated ingredient systems can help trace ingredients from the start of the process until the finished product. A fully integrated system can keep necessary documentation and also work with your labeling system.
Pet Food Process Improvement Assessments
Go through pet food processing improvements step by step, and compare all the costs and expenses equally. Remember to include not only upfront investment costs on one side of the equation, but also maintenance, training, or installation. On the other side, include all the benefits you’ll receive, such as process speed improvements, reduced waste, decreased downtime, and lowered maintenance costs long term. Take a look at the process improvements and efficiency upgrades that present the biggest opportunities first. Equipment or processes that are causing waste and delays should be examined first, as these will present the biggest opportunities for improvement.
With the right systems, equipment upgrades and process speed coordination, you can optimize the most essential aspects of your pet food processing facility. Assess each process first to find where opportunities exist. Prioritize each improvement, and take them on step-by-step, as opportunities become available.
Contact us today for any questions on pet food processing equipment, improvements, or more.