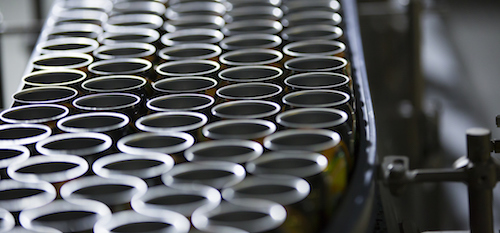
Choosing the right alloy for your custom fabrication is the first and, often, the most important step in creating a high-quality product or component. There are many factors to consider when choosing a metal alloy for your fabrication, and there are many different alloys available. In this blog post, we’ve included a few of the most widely-used alloys, though there are hundreds of others.
Choosing the Right Alloy for Your Custom Fabrication Design
To choose the right alloy for your custom fabrication design, it’s important to know the task the component or product will be fulfilling, the environment it will be working in, and stresses it must withstand. Here are a few of the factors you should be aware of, though this is not an exhaustive list.
- Temperature: Many metals will warp or freeze up at high or low temperatures. Temperature considerations are especially important if your product or component will be working outdoors, or if friction or coolant will cause temperature swings.
- Corrosion resistance: All metals corrode to some extent, though some alloys are much more resistant to corrosion than others. If your product or component will be in contact with moisture, salts, acids or alkalis it’s important to consider an alloy that will resist corrosion.
- Durability: There are many different types of durability. For example, some alloys are highly resistant to bending or warping, but will snap past a certain threshold, while others are made to bend under pressure. Consider the amount of force or weight that the alloy must withstand, as well as the type of force it will face.
- Weight: If a component in a machine is too heavy, it will require the rest of the machine components to work harder. It’s important to know just how heavy the component or product can be before it becomes impractical.
- Fabrication process: Some alloys are more difficult to weld, machine or form, which will complicate the fabrication process. Knowing how the product will be fabricated can help to choose the right alloy.
- Cost: Materials cost is always a factor. If finding the right alloy means overextending your budget, you’ll need to reassess. Keep in mind that cost isn’t limited to the initial cost of the materials themselves, though. Cost may also include a component’s upkeep or cost of replacement if it’s corroded or damaged.
Many of these factors involve a balancing act. For example, metals with high durability tend to be heavier and more expensive. Metals with high temperature thresholds or corrosion resistance can be more difficult to work with, and more expensive and time-consuming to fabricate. This is why it’s helpful to be specific about how you need the alloy to perform, so you can balance all of these elements together.
Types of Alloys in Metal Fabrication
There are hundreds of different types of metal alloys. Combining different metals in different amounts will yield different results, and new alloys are being developed all the time to take on complex challenges. The most commonly used alloys in metal fabrication generally contain steel (which is itself an alloy of mainly iron and carbon), aluminum, and nickel.
Stainless Steel
Stainless steel is an additional extension of the steel alloy, and it is one of the most popular metal fabrication materials. There are many different types of stainless steel. Stainless steel may contain additional chromium, nickel, tungsten, titanium, molybdenum and many other metals. Some very specific types of stainless steel used in military applications even contain depleted uranium. These additional metals help to determine the unique properties of each stainless steel type.
304 Stainless Steel
SAE 304 stainless steel, also known as A2 stainless steel or 18/8 stainless steel, is the most common type of stainless steel. It’s made from chromium, nickel and steel, and has a number of versatile characteristics that make it suitable for many different applications.
304 stainless steel has a clean, shiny appearance, high corrosion resistance, decent durability and it’s easily formed and welded. This makes it a go-to alloy for custom fabrication, appliances, food processing equipment, consumer goods, pipes, fasteners and many more. There are a number of sub-types of 304 stainless steel using varying amounts of carbon, which can change its temperature resistance, corrosion resistance, and tensile strength to meet the needs of specific applications.
316 Stainless Steel
SAE 316L stainless steel, also known as A4 stainless steel or marine grade stainless steel, is similar to 304 stainless steel, but with some differences in composition and function. This steel alloy contains molybdenum in addition to chromium, nickel, and steel, as well as small quantities of silicon, phosphorus and sulfur. These additions make it more resistant to corrosion.
Just like 304 stainless steel, there are different sub-types of 316 stainless steel which contain varying levels of molybdenum, carbon and nitrogen. These differences change the strength and corrosion resistance of each alloy. This type of steel is ideal for environments with high corrosion, such as chemical refining, textile bleaching and coloring, surgical implants and applications near or in seawater.
Aluminum Alloys
Aluminum alloys are another popular choice for many metal fabrication products and components. Like steel, aluminum alloys can be mixed with many other metals, including nickel, magnesium, titanium, cobalt, lithium, and many more. Each unique alloy presents different advantages and disadvantages.
The main advantage of aluminum alloys is their lightweight composition. This makes aluminum alloys a preferred choice for many automotive and aerospace applications. Aluminum is also relatively inexpensive and it can be used in extrusions, adding flexibility in the manufacturing process. However, there are some drawbacks; aluminum alloys are generally not as durable as stainless steel, and they’re more sensitive to stress and heat.
Nickel Alloys
Nickel alloys also present unique benefits for some custom fabrication work. These alloys most commonly contain metals similar to aluminum alloys and stainless steel alloys, like chromium, molybdenum, iron, copper and titanium, among others.
Nickel alloys are used in some of the most demanding applications. They are very resistant to thermal expansion and electromagnetic interference, which makes them ideal for sensitive measurement instruments and electromagnetic shielding. Many nickel alloys are also highly corrosion-resistant against common corrosive substances like seawater and even uncommon, highly corrosive substances like hydrochloric or sulphuric acids. This high resistance to temperature extremes, extremely corrosive substances, and mechanical force puts many nickel alloys in the category of superalloys.
There are many more unique alloys used in all types of different applications. Stainless steel alloys are often the right alloy for custom fabrication work, though not always. If you are working with a challenging application with high temperatures, corrosive materials, weight constraints, or other obstacles, there are other metal alloys that can meet your needs.