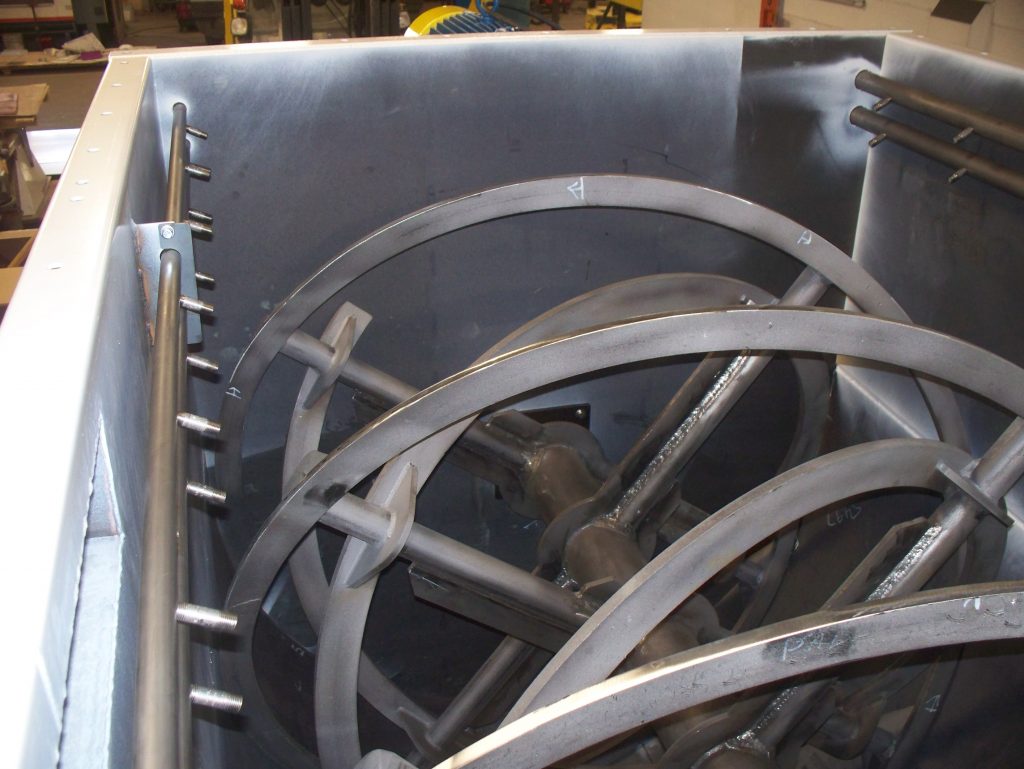
The type and number of blenders you choose for your process will play an important role in how fast and how well your recipe is mixed. There are a number of different ways to customize your ribbon blender, and it can be difficult to choose the right model. Here’s a few factors that will help you choose the right ribbon blender for your ingredients and process. We’ve updated this blog post in 2022 to provide more information and help you get the best ribbon blender.
7 Considerations to Customize and Select a Ribbon Blender
1. Size and Volume
The volume and profile of the ribbon blender are the most important aspects to consider when selecting your ribbon blender. This will depend on the amount of material you are mixing, as well as the speed with which it must be mixed. In some cases, a very large blender might be suitable. In other cases, multiple smaller blenders can help you optimize the process. With multiple blenders, you can avoid a shut-down if something goes wrong, and you can also dramatically reduce the time needed to mix a batch.
The ribbon mixer should be filled to its swept volume to get the most efficient mix. The swept volume is the area occupied by the agitator. In order to get the best mix in the shortest amount of time the mixer profile is also important. The length of the mixer should not exceed 2.5 times the diameter of the agitator. Consider the length, width, height and volume of the vessel, as well as the agitator size, to customize your ribbon blender to the right size.
Design the ideal system for your ingredients.
Download The Guide: 8 Key Equipment Decisions to Perfect Your Dry Mix
2. The Ribbon or Agitator Type
A ribbon mixer successfully mixes materials by agitating them with a corkscrew-like metal blade. The outer helix of the ribbon moves product in one direction, while the inner helix of the ribbon moves the material in the opposite direction. This movement of material from one end to the other provides a fast but gentle mixing action. If more shear is needed to change the ingredients’ characteristics, then the mixer can be run at a higher speed or other devices can be added to the mixer, such as high-speed choppers.
Some types of materials may work better with a mixer that uses paddles for the agitators instead of ribbons. This can be true of ingredients that have a high liquid content or those that are sensitive to shear. Selecting the right ribbon or agitator type is important for customizing the right ribbon mixer, or another type of mixer. The type of agitator you will need will depend on your ingredients, as well as the mixing time and mixer profile.
The following factors can help you determine what type of agitator to use:
- Shear: If you are working with dense or viscous materials, your agitator may need a higher degree of shear. The speed of the agitator and the tolerances between the mixer body and agitator can increase the amount of energy that goes into the mix. Generally, more shear will require more horsepower.
- Friability: Contrastingly, if your materials might easily break as they’re being mixed, you might use a gentler agitator, such as a paddle mixer. Mixing at a lower speed will also help this process, which we’ll discuss later in the post.
- Single or double ribbons: Using mixers with two sets of agitators will decrease the overall mix time required for the process. These mixers use ribbons, paddles, or sometimes a combination of the two. Using double agitators will also increase the horsepower required.
3. Mixer Construction Materials and Finish
Ribbon mixers are made from both mild and stainless steel. The materials of construction will depend upon the ingredients that are being mixed and the how those ingredients are going to be used. For example, in the case of food-grade ingredients, the mixer should be stainless steel with special finishes so that it can be easily cleaned and sanitized. If the ingredients are corrosive, then stainless steel would also be a good choice, since mild steel would be dissolved by the ingredients over time. However, your materials or process may require other materials or finishes. If your materials are not susceptible to foodborne illnesses, these finishes might not be necessary.
Quite often, the exterior of the mixer or non-contact areas of the mixer can be made from mild steel and painted. The interior of the mixer is usually not painted, since it could contaminate the ingredients being mixed. A mixer can also be lined with a material to enhance it’s performance. This is typically seen when a material is abrasive and would prematurely wear out the interior parts. Or, if you are working with corrosive materials, another finish may be required. Your ribbon mixer can be customized with a range of materials, finishes and paint to suit your facility.
The following are popular materials and finishes in ribbon mixers:
- Various weld finishes from standard welds to sanitary
- Industrial enamel paint or epoxy paint
- Stainless steel food grade
- Abrasion resistant linings such as ceramic and UHMW plastic
4. Horsepower
Most ribbon mixers operate at around 20 RPMs, though mixers with dual agitators or wider ribbons will require more power. A general rule of thumb for medium-density material in a single-agitator ribbon blender is 10hp per ton of material being mixed. To select a mixer that is both effective and efficient, use a motor with the appropriate horsepower. The supplier of the mixer can help with motor sizing and type. Selecting a motor that is too powerful can mean adding extra expenses, but underestimating the motor power can mean that the mixer cannot be started under load.
5. Discharge Gate
How your ingredients exit the mixer is also important when customizing your ribbon blender. The cycle time and downstream processes will partly determine which ribbon blender is best. Some processes may require complete, immediate discharge. In this case, a full-length drop bottom discharge gate would be ideal. Other processes may require gradual discharge or a tighter seal, and a slide-gate may be better in these cases.
The most common types of discharge gates for your ribbon mixer are:
- Drop bottom: A drop bottom discharge gate will fully release materials in the mixer immediately. Though these gates work quickly, getting a tight seal can be difficult, especially when working with fine powders. This quick discharge can cause dust to escape into the air, so proper venting of the mixer is needed.
- Pneumatic Slide Gate: A slide gate will allow a set amount of material to escape, which can be helpful for measuring, batching, or bagging processes following mixing. These will also have a tight seal to prevent powder from escaping.
- Multiple Slide Gates: If you are looking for a faster discharge rate as well as a tight seal, you can use multiple gates to speed up the process, while still preventing powders from escaping.
6. Ingredients Characteristics
A list of ingredients characteristics will help you and your engineering partners design the ideal ribbon mixer. Different types of ingredients will mix and separate faster, may damage the mixer, or may be damaged by the mixer. A list of ingredients that you’re using as well as the key characteristics of each ingredient will help to ensure that the ribbon blender is designed to mix your recipe properly.
Knowing the following ingredients characteristics will help you design the ideal ribbon blender:
- How many ingredients you’re using
- The type of ingredients, including powders, liquids, or pastes
- Bulk density
- Adhesion
- Freezing and melting point
- Particle size and variation
- Friability and shear sensitivity
- Flammability or explosive qualities
7. Facility Requirements and Constraints
Your ribbon blender must fit in your facility and fit alongside your existing equipment. Making a few notes about your facility requirements and constraints will help to ensure that your ribbon mixer fits perfectly with your existing equipment. Making notes about your production needs will also help you determine your mixing time, and how fast you need your mixer to operate. This can also help you determine the mixer profile and design, as well as how many mixers you might need to meet your optimal production time.
It’s helpful to know and record the following information about your facility requirements and needs.
- The total space available for the ribbon blender
- The surrounding machines and equipment
- Weighing devices that might be used upstream or downstream from the mixer
- How much you need to mix, how quickly
- Flammable, explosive, or other safety concerns
Choosing the right ribbon blender and customizing features to suit your process and materials means getting the perfect mix. With consistency and accuracy built into your process, you can eliminate many concerns and problems both upstream and downstream. Work with a supplier who can help you customize these features to suit your process and provide testing to ensure you have the right fit. If you’re interested in ribbon mixers, APEC has horizontal ribbon mixers suitable for nearly every application.
Optimize your design
Download The Guide: 8 Key Equipment Decisions to Perfect Your Dry Mix
Industry Advantage: APEC’s Horizontal Ribbon Mixer
APEC’s in-house engineers and fabricators have successfully designed an innovative, high-quality horizontal ribbon mixer for processing animal feed, pet food, snack foods, and more. We take great pride in our equipment’s capabilities, and we are confident that our horizontal ribbon mixer will give your processing plant the advantage it needs.
A Solid Foundation
The end-to-end mixing action of a double-ribbon agitator ensures an even blending of ingredients, leading to a more balanced and higher quality mix. Solid spokes mounted to a durable center shaft eliminates the chain, which simplifies maintenance, unlike chain and sprocket arrangements that are found on other mixers. The main shaft is supported by either a ball bearing flange or spherical roller bearings.
This solid foundation provides an essential horizontal ribbon mixer base for many different industries. A variety of customizable options allow you to select a ribbon blender that will work best for your ingredients, facility and needs.
Customizable Options
As previously mentioned, there are many aspects to consider to configure a ribbon mixer that will work best for your needs. Building off the solid foundation and standard features, you can customize the APEC horizontal ribbon mixer in many ways to suit your needs.
APEC offers a wide range of custom horizontal ribbon mixer options, including:
- Ribbon Mixer Size: the ribbon mixer dimensions can be customized to suit your facility and the space you have available, as well as the surrounding equipment.
- Capacities (Swept Volume): The ribbon mixer profile, capacity and speed are both important considerations to ensure that your ribbon blender can properly mix your ingredients in the optimal time frame.
- Horsepower: The mixer size and swept volume, as well as the ingredient characteristics, will impact how much horsepower your mixer will need.
- Discharge gate: Choose a discharge gate that works best for your surrounding equipment, including a full-length drop bottom, standard pneumatic-end slide gate, optional center-pneumatic slide gate, or multiple slide gates.
- Finishes: Choose from standard weld, industrial enamel, or stainless steel food grade, as well as any paint specifications.
- Motor: With the horsepower and mixing capabilities calculated, you can get a motor that is energy efficient and effective. The motor can also be explosion-proof, which can be particularly helpful when working with powders or dangerous ingredients.
- Weighing: The ribbon blender can integrate with a load cell weighing assembly and other weighing instruments as needed.
APEC has horizontal ribbon mixers suitable for nearly every application.With the right customizations, your horizontal ribbon mixer will run more efficiently, provide higher output, and require less maintenance. This allows you to focus less on your machine and feel assured that your product meets your (and your customers’) high standards and expectations. With each component being custom designed, engineered, and fabricated in-house, you’re sure to get exactly what you need to consistently deliver a product you can be proud to offer. To learn more about how our innovative and durable horizontal ribbon mixer can give your processing plant an advantage, contact APEC today!